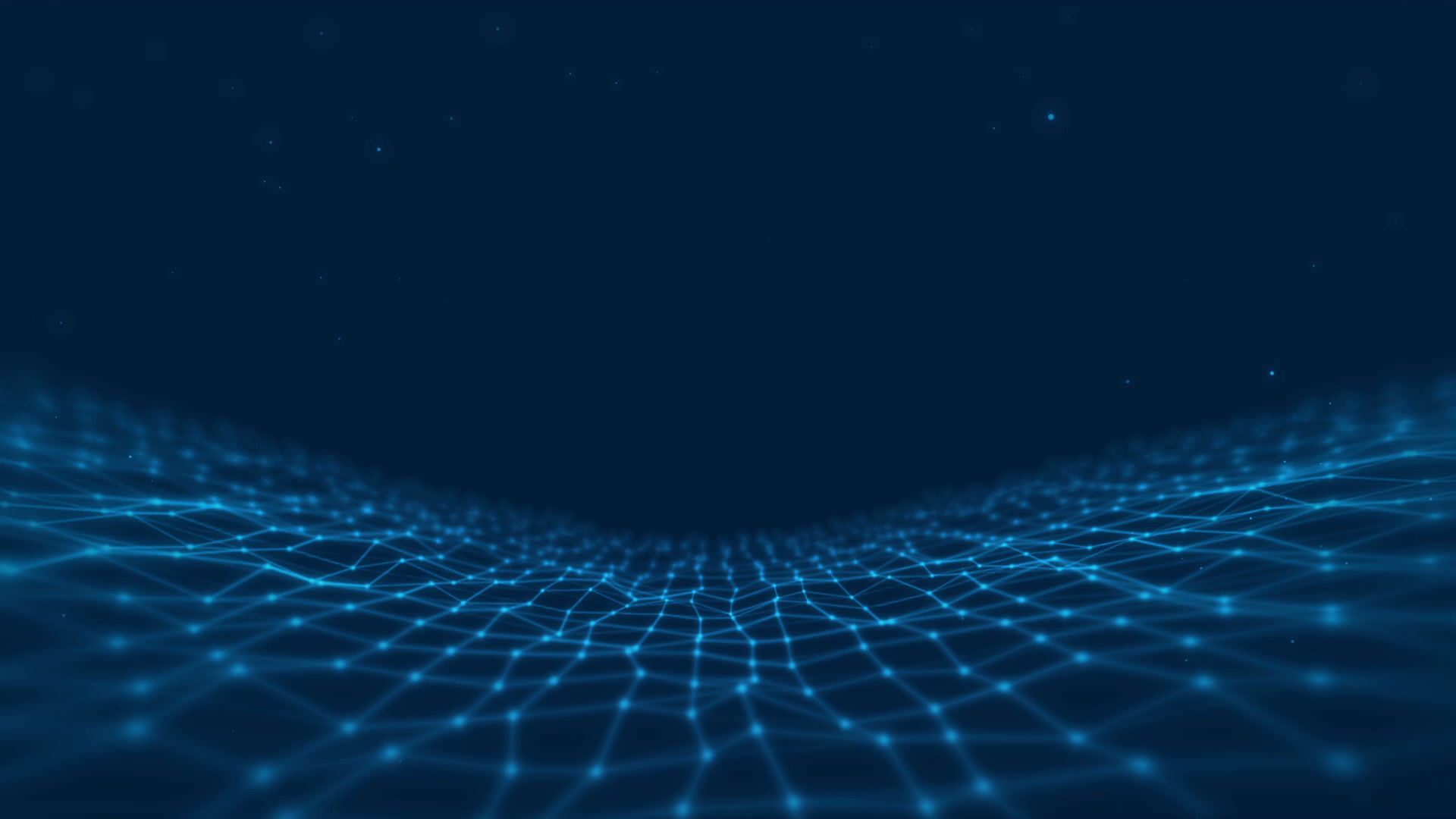

MAPS Laboratory
Materials’(Ma) Process(P) - Structure(S) correlations Laboratory
Welcome to

Department of Metallurgical and Materials Engineering
Indian Institute of Technology Patna (IIT Patna)
Shape/Consolidation Strain
Recently, we have noticed an interesting phenomenon involving the processing of ceramics. We have termed this phenomenon as ‘shape strain’ or ‘shape/consolidation factor’. Although we first observed this phenomenon in doped zirconia ceramics, the later influence of this factor has also been found in many other associated systems (oxides, carbonates, etc.). Over the last five-six years now we have published a handful of articles on this topic and now decided to provide a brief outline of the effect in a question-and-answer (Q&A) format for quick understanding. More details on this theme of work can be found in the below mentioned references.
-
Scr. Mater. 190, 52-56, 2021. (https://doi.org/10.1016/j.scriptamat.2020.08.039)
-
Materialia 25 (2022): 101527. (https://doi.org/10.1016/j.mtla.2022.101527)
-
J. Am. Ceram. Soc. 2023;1–12. (https://doi.org/10.1111/jace.19607)
-
Cryst. Growth Des. 2023, 23, 11, 7754–7762. (https://doi.org/10.1021/acs.cgd.3c00534)
Benefits of Shape Strain:
-
J. Am. Ceram. Soc. 2021;104: 3497-3507 (https://doi.org/10.1111/jace.17683)
-
J. Mater. Sci. 58, 17175–17187 (2023) (https://doi.org/10.1007/s10853-023-09133-8)
Q1. How did the idea of “shape strain” evolve in the first place?
Ans. Compared among the grain size of a sintered body with respect to the particle size of calcined powders (heat-treated at the same sintering conditions), the microstructural evolutions in the sintered body and calcined powder should not be the same.
For the case of CaO-doped zirconia ceramics (Scr. Mater. 190, 52-56, 2021), we noticed a massive size reduction in the sintered ceramic (compared to the calcined CaO-doped zirconia powders under the same sintering temperature conditions). This suggests that the shaped ceramic experienced a hindrance during sintering that eventually restricted the growth of grains. In our first report (Scr. Mater. 190, 52-56, 2021), we tried explaining this using a factor labelled “consolidation factor.”
Q2. Can you explain “shape strain” in a more generic way?
Ans. For all materials that depict a size-induced phase transformation, a critical grain size criterion is mandatory. If such a critical grain size can be ensured for any sintered ceramic body, its phase transition can also be averted. Let us take a material with β1 phase in starting powders, as shown in Figure 1. When the powder (with phase β1) is heat-treated through path-1, it converts to a new phase β2 (and remains as powders). On the contrary, the same starting powder when heat-treated through path-2 following the same heating condition (via pressing and conventional sintering), yields a new phase β3. The consolidation factor (via pressing and sintering) is responsible for this difference. For the case of zirconia (Scr. Mater. 190, 52-56, 2021), we have presented such an idea of mitigating the monoclinic phase (β2) which is known as one of the most detrimental phases for technological applications.
Fig. 1 Difference of phase evolution with (path-2) and without (path-1) consolidation factor.
Q3. From this answer, it seems the “shape strain” factor may/should have a strong connection with the nanoscale. Is this true?
Ans. In fact, this is exactly what we have seen for the CaO (3-4 mole %) ZrO2 systems. Where we saw the tetragonal phase, stability is restricted below a critical size of 100 nm (approx). However, later on, while doing experiments with other oxides like TiO2, BaTiO3 (Materialia 25 (2022): 101527), and carbonates (Cryst. Growth Des. 2023, 23, 11, 7754–7762), we have not observed any such strong nano connection. Therefore, there is no strong ground to think this effect is only confined to the nanoscale.
Q.4 How different is the ‘Shape Strain’ effect from any other pressure-induced phase transformation?
Ans. Very different. This has nothing to do with popular pressure-induced phase transitions examples. After the samples were uniaxially pressed and checked by XRD, no phase change/alteration was observed. Please also note that the materials that undergo a phase change upon application of pressure always need high pressure (at least > 10 GPa). In this case, we are talking about a pressure range of 300-800 MPa. The whole story is evolving only after sintering/consolidation. In other words, diffusion phenomena have a huge role to play here.
Q5. The size effect (in nano), doping in any ceramic’s matrix, and thermal artefacts, etc.-all these are expected to induce strain in the lattice. What is NEW about the shaping-induced strain?
Ans. The total strain (εTotal) in the sintered ceramics may be expressed using the following equation:
εTotal = εDoping + εSize + εThermal + εShape ……………(1)
Where ε Doping, εSize, and εThermal represent strain contributions due to doping, nanosize, and heat treatment, respectively; σShape denotes the consolidation strain induced in the ceramic as the powders are compacted and heat treated for making a 3D bulk shape. The equation itself denotes that shaping-induced strain is always present in any ceramic body by virtue of the way they are shaped. However, for the case of calcia-stabilised zirconia the effect of shape strain was clearly understood since the retention of a phase pure tetragonal ceramic would never be possible without the shape strain effect. Therefore, it will be safe to say that: although a shaping-induced strain is omnipresent in the final ceramic body, their effect may only be realised in specific cases. For the calcia (CaO)-stabilised zirconia system, this effect is important as it is giving a new product that no one could think to exist fifty years back.
Q6. When anyone processes a three-dimensional bulk body via pressing and sintering, eventually, every shaped body will have some strain. Why, then it suddenly becomes important to the context of the matter examined by you all?
Ans. Please refer to our answer for question number 5. Hopefully, it will resolve your query.
Q7. Carbonates involving alkaline earth metals are known for their parity in their behaviours. In this connection why the shape strain behaviour in BaCO3 is special? Have you tried to investigate the same phenomenon for CaCO3 and SrCO3?
Ans. Yes, we have. And surprisingly we don't see any effect of a shape strain phenomenon for CaCO3 and SrCO3. Please also note that compared to alkaline earth metal carbonates, both barium and strontium carbonates are very stable carbonates at high temperatures. Even then, this effect was only observed for BaCO3.
Q8. Whatever you saw in BaCO3, it could be due to moisture-induced phase transition. If it is so, why should we be bothered anyway?
Ans. Yes, we are aware of the fact that water vapour/moisture has a huge role in transforming a tetragonal to a monoclinic phase during low-temperature degradation in zirconia ceramic. However, for the present case, we have definite proof to conclude that what we have seen in BaCO3 is not induced by moisture.
In the case of BaCO3, the manifestation of the ‘shape strain’ effect by virtue of variation in X-ray diffraction pattern in the cooled pellet is only evident when the heat-treatment temperature is above the orthorhombic (space group: Pmcn) to trigonal (space group: R3m/ R-3m) transformation temperature (>820 °C). The consistency of XRD patterns (Fig. 1) of powder and pellet (of BaCO3) in particular heat-treatment temperature, below the phase transition temperature (i.e. below TOrthorhombic →Trigonal) is a clear demonstration of this (Cryst. Growth Des. 2023, 23, 11, 7754–7762).
Fig. 2. S and C denote the pellet and powder samples, respectively, and the corresponding number depicts the temperature value (in °C) at which the sample was heat treated. Numbers 1, 2, and 3 show numbers of experiments that have been carried out in similar conditions (to demonstrate results repeatability). X-ray diffraction plot of (a) S750, (b) S800, (c) C750, (d) C800.
As the diffraction patterns are repeatable (Fig. 2) at a particular temperature (below TOrthorhombic →Trigonal, i.e. ~820 °C), the manifestation of shape strain is not observed. Had this effect originated from the adsorption of water vapour/moisture (and not due to ‘shape strain’), the alteration in the diffraction pattern would have also been present for the samples heat-treated at a lower temperature than TOrthorhombic →Trigonal (i.e.750 °C and 800 °C). This concludes that: the effect of shaping/consolidation and heat treatment in the vicinity of phase transition is solely responsible for the observed phenomenon.
Q9. Why do you attribute a ‘strain’ parameter to this phenomenon? Have you tried to measure it? I mean to say, will Shape Strain be calculable and measurable?
Ans. We attribute a strain parameter since it is obvious that when the powders are pressed automatically, it will experience the strain. This strain is always present in a sintered ceramic. However, when the material responds to this strain in a unique or strange way, the science becomes interesting. The ceramic body can typically respond to this strain in two broad ways, (1) either accommodate this strain in refining the grain sizes (this is what we observed in calcia doped zirconia system) or (2) release this strain facilitating a phase transition (as observed in BaCO3).
This strain can be measured with some legitimate approximation. Please refer to the following equation:
εTotal = εDoping + εSize + εThermal + εShape ……………(1)
When a dopant is introduced for the sintering of ceramic systems, both εThermal and εShape would increase. Even εDoping would also increase as the temperature is increased during sintering. One easy approximation, however, would be to measure this doping-induced lattice strain in a free powder (that would be used for sintering) system only. If the refined size (of the matrix) is in nanoscale, εSize would change with temperature. Please note that both εDoping and εSize would have the capacity to induce prominent lattice strain in the ceramic and they would also have different kinetics with temperature. εThermal can be approximated by calculating the thermal strain at room temperature. Thus, εShape can be calculated by subtracting εDoping, εSize, and εThermal from εTotal.
Q10. Since you only said about its importance for doped ZrO2 ceramics, could it be possible to observe the effect only when doping is present? Or, if doping is present, how significant the effect would be?
Ans. Yes. This is what we thought in the initial days when we first saw this dramatic effect in calcia-stabilised zirconia. Please note that this critical size factor, as mentioned by Garvie (J. Phys. Chem. 1965, 69, 4, 1238–1243) primarily focused on the tetragonal to monoclinic transformation in zirconia bodies. Therefore, we also tried to confine our studies to lower amounts of doping. Please note that among all the tried/examined dopants, the CaO dopant showed this effect most prominently since it could control the grain boundary mobility of zirconia in an effective manner. Interestingly, other researchers have also observed this (without explicitly calling this effect as ‘shape strain’). Please refer to Table 1 (taken from M. Turon-Vinas et al., J European Ceram Soc. 38 (6) 2621-2631, 2018). Here, the researchers noticed a more than 300% reduction in the average grain size in a ceria-doped zirconia ceramic as the CaO co-doping was increased from 0 to 3%. At that point, we also thought this effect to be an artefact of size-dependent phase transformation in oxides (but not in powder but in sintered ceramic 3D form).
Table 1. Composition, density, grain size and constituent phases of the ceramics sintered for 2 h at 1500 ºC (J European Ceram Soc. 38 (6) 2621-2631, 2018).
Prof. Navorotsky’s group (ChemPhysChem, 12 (12) (2011), pp. 2207-2215) has conducted detailed research on this aspect but every time the system was free powder. For the case of CaO-doped zirconia, we see the same effect but are governed by the grain boundary mobility control of the CaO dopants.
Q11. The effect seems to be very mundane. How come nobody else has observed or reported this before?
Ans. Yes. The effect is mundane indeed as every bulk ceramic (when processed by a solid state route) has to go through this pressing operation followed by sintering. However, this processing operation being the same every time, it becomes really interesting when the outcomes differ (specially in the context of phase evolutions). Nearly three months after we published this effect in CaO-doped zirconia, Prof. Christopher Schuh’s group at MIT published a very similar effect for ceria-doped zirconia bodies, where they measured overall shape strain using different strain components. The figure below (Fig. 3) clearly points out the difference in phase development in powder and pellets of the same ceria doped zirconia systems (J Am Ceram Soc. 104 (2) 1156–68, 2021).
Fig. 3 Difference in phase development in powder and pellet of the same ceria-doped zirconia systems
(J Am Ceram Soc. 104 (2) 1156–68, 2021)
Hence, the effect of strain getting accumulated due to shaping is always present in the ceramic bodies. Sometimes, the shaped body accommodates this strain by refining the grain size (e.g. for the case of CaO stabilised zirconia systems). In some other cases it tries to find a balance between multiple pathways of energy release kinetics and ends up showing bizarre phase developments (Cryst. Growth Des. 2023, 23, 11, 7754–7762).
Q12. Besides being just a phenomenon of scientific interest, why should the ‘shape strain’ factor be important anyway?
Ans. Well, this is important because it had the potency to give us a product that nobody could imagine fifty years back. Please refer to the image below to acknowledge that CaO-doped zirconia bodies were only treated as partially stabilised zirconias ( J Phys. Chem. Solids, 34, 1873-1878, 1973) and up to 16 mol.% would need to stabilized the cubic form of zirconia. In those days, CaO-doped tetragonal zirconia would never be free and would always consist of a sufficient/significant amount of monoclinic phase. It is only the shape strain factor due to which the CaO-doped phase-pure tetragonal zirconia products are achievable even with minimum (3-4 mol.%) CaO doping (J Am Ceram Soc. 2021;104: 3497-3507). The image below (Fig. 4) depicts a change in the trajectory of zirconia based research over a period of ~ 50 years.
Fig. 4. Trajectory of research for last Fifty years on CaO-doped ZrO2 ceramic
The CaO-doped zirconia products are:
● Having very high hardness (~14.8 GPa) and indentation toughness (~5.6 MPa). In Fact the toughness values are way better than the traditional tetragonal YSZ systems. (J Am Ceram Soc. 2021;104: 3497-3507)
● Having much better LTD properties compared to tetragonal YSZ compositions (J Am Ceram Soc. 2021;104:3497-3507).
● Having better thermal shock resistance than industrially popular YSZ components (J Am Ceram Soc. 2023;1–12).
● Having greater thermal conductivity than industrially popular YSZ compositions (J Am Ceram Soc. 2023;1–12).
● Having better translucency compared to most of the tetragonal zirconia compositions known till today. We have also shown that cubicity is no longer a prime requirement anymore for obtaining translucency in zirconia bodies
(J Mater Sci 58, 17175–17187 (2023).
It's now therefore important to bring this product to market.
Q13. How generic the shape strain effect is expected to be?
Ans. We do not have a specific answer to this at this moment and that’s why it needs to be investigated for many other systems. Each time we are performing the same action (i.e., uniaxial pressing and sintering), but the outcome is different – not within different systems but even in the same system with different dopants. For example, in zirconia ceramics MgO and CaO behave in a similar way and eventually it was the CaO dopant which showed the shape strain effect prominently (Scr. Mater. 190, 52-56, 2021). However, for BaCO3 it gets reflected in the form of an enhanced energy release rate (during trigonal to orthorhombic transformation) which later on became the major factor for a staggering difference between the phase evolution in pellet and BaCO3 powder heat-treated at same temperature (Cryst. Growth Des. 2023, 23, 11, 7754–7762).
Q14. Many of us visualize strain always with a deformation (specifically via load). Where exactly in terms of deformation is happening inside the materials?
Ans. Let us consider any melting process of a metal. As the molten metal crystalizes, it will most likely be polycrystalline with prominent grain boundaries. All the grain boundary triple junctions are sources of strain (lattice). Now if anyone starts contemplating the idea of an ‘external load-induced deformation strain' here – there is no such thing. But there is strain. In fact, for thin film epitaxy, it is the lattice misfit strain that rules the nature/extent of epitaxy (of the film). Again asking the same question [“where is the external load here?”] has no relevance here. Having said all these, let us come to the point. The apparent sintering stress, σsa, can be calculated from Eq. (2) (Ceram. Int. 35 (2009) 3185–3194)
σsa=FL/π(rc.rc) ρ ......... (2)
where FL is the load to the load cell, ρ is the relative density, and rc is the cross-sectional radius of the specimen. Please note that this equation becomes too simplistic once (& when) it starts considering pressing and heating (in a furnace) as two separate processes. However, it starts to make more sense for the sintering cases where pressing and heating are conjugated (e.g., in the cases of hot pressing, HIP, SPS etc). For the present case, whenever we are discussing a ‘shape strain’ event, the strain usually has implications with lattice, grain boundary mobility etc. For a conventionally sintered ceramic, the transmitted pressure (during uniaxial/iso-pressing) in the ceramic body shows its manifestation in the form of different arrangements of grain boundary (post-heating). This change in microstructure is linked with an inherent strain in the lattice; the pinning (or drag) effects at the grain boundaries also facilitates this arrangement. Once such a change influences a phase transition, we get to see the direct influence of a ‘shape strain’ factor. Once this residual strain finds a release pathway, its kinetics may induce a difference in phase evolution behaviour (as we see in the case of BaCO3).
Appeal: In case you have also experienced similar issues while consolidating any materials, we welcome you to share your thoughts directly with us (anirc@iitp.ac.in, anirban.chowdhury@gmail.com). We will be happy to hear from you with a possibility of future collaboration/s.
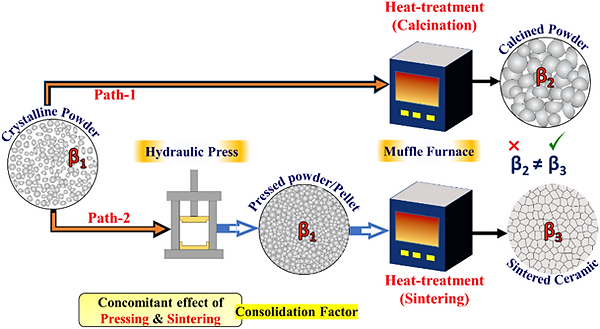
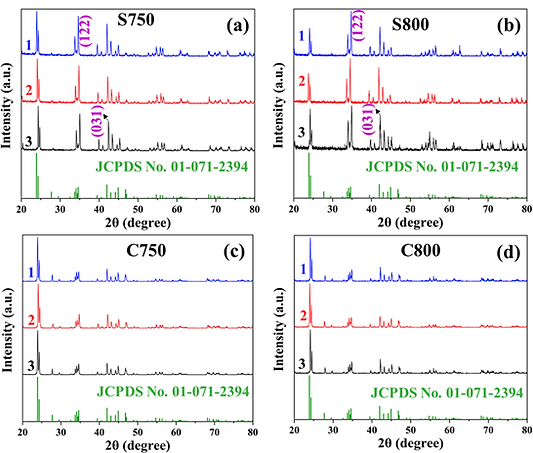

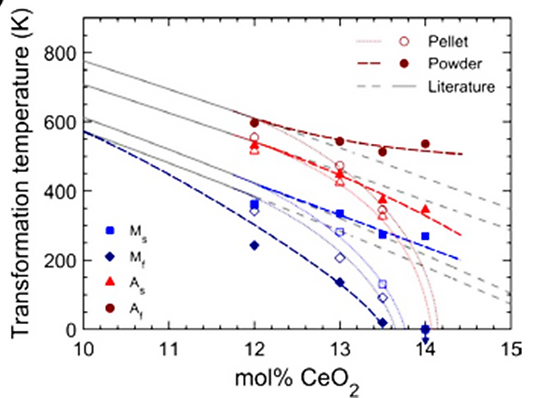
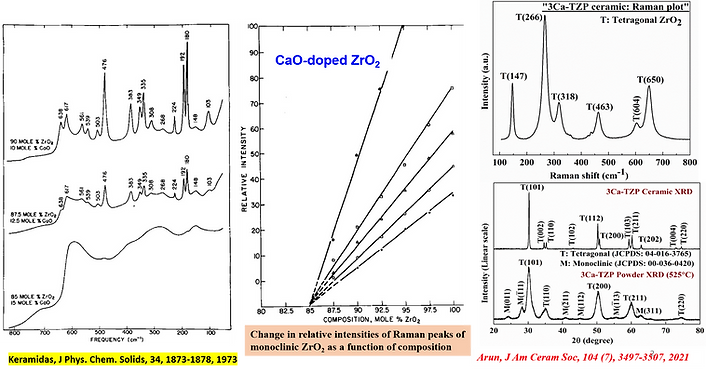